Safety & Environmental Management Systems (SEMS), are designed to prevent releases of oil, gas or chemicals that have the potential to cause loss of life or environmental damage due to catastrophic fires, explosions, or toxic exposures.
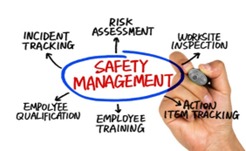
SEMS has been in effect as a mandatory requirement to operate in the United States Outer Continental Shelf since November 15th, 2010. This encapsulates all phases of offshore operations including drilling, production and covered pipelines.
The elements of SEMS as defined in 30 CFR § 250 are:
- General provisions for implementation, planning and management review and approval of the SEMS program.
- Safety and environmental information.
- Hazards analysis.
- Management of change.
- Operating procedures.
- Safe work practices.
- Training.
- Mechanical integrity.
- Pre-startup review.
- Emergency response and control.
- Investigation of Incidents.
- Audits.
- Records and documentation.
- Stop Work Authority (SWA)
- Ultimate Work Authority (UWA)
- Employee Participation Plan
- Reporting Unsafe Working Conditions
Having an effective SEMS program will benefit your company by:
- Improving mechanical reliability and regulatory compliance
- Strengthening your safety and environmental performance
- Mitigating risk
- Avoiding citations and fines
Safety Intelligence, LLC can develop a fit-for-purpose Safety Management Systems (Plan-Do-Act-Check). For companies with existing management systems, Safety Intelligence’s vast experience can assist in:
- Performing gap assessments against SEMS requirements (Compliance and Risk Management)
- Developing local assurance protocols for the site
- Mitigating corrective action items from your internal or 3rd party SEMS Audit
Contact us to discuss your needs, and together, we’ll tailor a solution.