Conscientious industries commit to protecting the health and safety of workers, neighbors and the environment in which they operate. Process Safety is one of the most important means to achieve this goal.
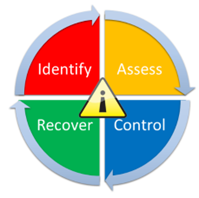
Process safety generally refers to the prevention of unintentional releases of chemicals, energy, or other potentially dangerous resources (such as dropped objects) during the course of their processes. Process safety involves, for example, the prevention of leaks, spills, equipment malfunction, over-pressures, over-temperatures, corrosion, metal fatigue and other similar conditions. Process safety programs focus on identifying these hazards, and ranking them appropriately using various risk management methods. These methods identify the focus necessary for design and engineering, maintenance, dedicated procedures, and required personnel training.
Process Safety as outlined in 29 CFR § 1910.119:
- Employee Participation
- Process Safety Information
- Process Hazard Analysis
- Operating Procedures
- Training
- Contractors
- Pre-Startup Safety Review
- Mechanical Integrity
- Hot Work Permit
- Management of Change
- Incident Investigation
- Emergency Planning and Response
- Compliance Audits
- Trade Secrets
Having an effective Process Safety Management (PSM) and Risk Management Program (RMP) will benefit your company by:
- Improving mechanical reliability and regulatory compliance
- Strengthening your safety and environmental performance
- Mitigating risk
- Avoiding citations and fines
Safety Intelligence, LLC can develop a fit-for-purpose Safety Management Systems (Plan-Do-Act-Check). For companies with existing management systems, Safety Intelligence’s vast experience can assist in:
- Performing gap assessments against PSM and RMP requirements (Compliance and Risk Management)
- Preparing for 5 year validations (Process Hazard Analysis, Hazard Assessment, Risk Management e-submit)
- Developing local assurance protocols for the site
- Conducting a Management of Change (MOC) review
- Facilitating Process Hazard Analysis using appropriate industry recognized methodologies
- Mitigating corrective action items from your internal or 3rd party audits
Contact us to discuss your needs, and together, we’ll tailor a solution.